Five topics down, two more to go. Our ongoing series on the total cost of ownership (TCO) of durable industrial labels has explored the following thus far:
Inventory management is next on our list. In the blog post that follows, we explain how inventory management practices play a role in the total cost of ownership (TCO) of durable industrial labels.
Inventory Management of Durable Labels
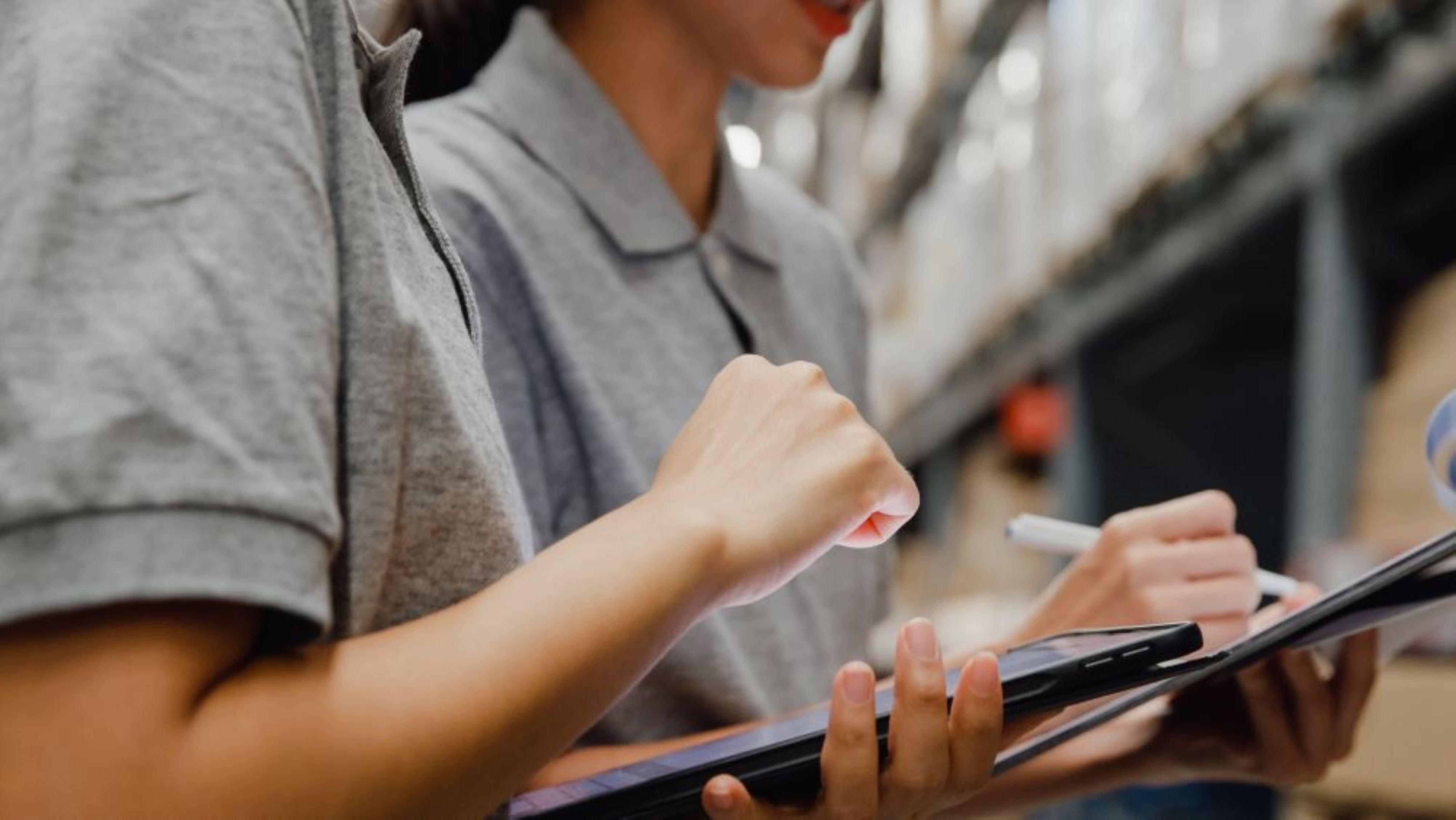
In simple terms, efficient inventory management means always having the right quantity of labels on hand at all times. You should strive to have enough stock to meet your current and future demand, but not so much that it leads to overstocking.
One way to achieve this is to maintain an accurate record of inventory levels through inventory tracking systems. These systems can be manual or automated and help you determine when you need to reorder. A more difficult area to manage is unplanned demand. It takes a highly skilled supply chain analyst to review past demand data and properly manage for unplanned demand.
Manage line-down risk
One of the most significant cost-saving strategies in label inventory management is balancing the risk of out-of-stock and line-down situations against the cost of rush orders and obsolescence risk of overstocking. It is essential to avoid situations where you're out of stock or don't have enough labels to meet production requirements. Few things drive up total cost of ownership more dramatically than an idle assembly line. To avoid line stoppages:
- Maintain a buffer inventory of critical labels.
- Implement proactive maintenance schedules to prevent equipment failures.
- Establish clear communication channels between production and inventory teams to monitor label stock levels in real-time.
On the other hand, overstocking can lead to high inventory costs and lost revenue from product obsolescence. By managing your inventory levels efficiently, you can find the right balance between out-of-stock risks and overstock risks. One method you can use is demand forecasting, which will be discussed next.
Use insightful forecasting
The third key consideration is demand forecasting, which is an essential component of efficient inventory management. It involves predicting future demand for industrial labels based on past sales data and market trends.
Done right, demand forecasting allows you to plan your inventory levels so you have the right quantity of labels on hand when they are ultimately needed. This approach helps you avoid stock-out scenarios and rush delivery charges while ensuring that your warehouse doesn't have excess stock of slow-moving products. Be sure to do the following:
- Analyze historical usage data to identify trends and seasonality.
- Collaborate with suppliers and customers to gather insights on upcoming changes in demand.
- Invest in forecasting tools and software to improve accuracy.
Take steps to reduce obsolescence
Obsolete labels can lead to significant financial losses a variety of ways. Products that are mislabeled jeopardize the brand while labels that are unusable must be destroyed, driving up the cost of an important manufacturing component. To reduce obsolescence:
- Regularly review and adjust label design and content to accommodate changes in branding or regulatory requirements.
- Use an inventory management system that tracks label expiration dates to prevent using expired labels.
- Consider on-demand label printing to reduce the need for large, pre-printed label runs that may become obsolete.
Minimize rush orders
Manufacturing environments are dynamic and rush orders sometimes become necessary. However, frequently relying on rush orders to keep the production line going adds needless cost due to expedited shipping and production. To minimize rush orders:
- Maintain a safety stock of frequently used labels.
- Implement just-in-time (JIT) inventory practices.
- Optimize lead times with suppliers to ensure timely deliveries.
Implement vendor-managed inventory (VMI)
Vendor-managed inventory (VMI) programs can be used to improve your inventory management processes. VMI is a collaborative approach in which the supplier takes on responsibility for monitoring and maintaining the buyer's inventory levels.
This model ensures that the buyer always has the required amount of inventory on hand, reducing the risk of stock-out scenarios. In turn, the supplier can optimize their production processes based on the buyer's order patterns, resulting in lower overhead costs for them. VMI is a true win-win for both parties offering a variety of benefits including:
- Reduced holding costs as suppliers optimize inventory levels.
- Improved order accuracy and reduced lead times.
- Enhanced visibility into inventory levels through shared data.
Shift to digital production
If your labels are currently being produced through a flexographic printing process, it may be time to consider a change. As noted in the first blog in this series regarding label converting processes, digital label printing offers several advantages.
- Reduced setup costs compared to traditional printing methods.
- On-demand printing capabilities, reducing the need for large label inventories.
- Customization and variable data printing for various label versions.
Standardize and rationalize your SKUs
Manufacturers often purchase multiple sizes and styles of labels when, with a little proactive planning, a single label construction could suit every application. Seek every opportunity to simplify your label inventory by standardizing label sizes and designs. Reducing the number of SKU variations can dramatically lower costs related to setup, storage and management.
Classify your labels by importance
Of course, not all labels warrant the same amount of managerial attention. The above action steps come into clearer focus when your labels are classified based on their relative importance:
- A-class labels are high-value and should be closely monitored.
- B-class labels are of moderate importance.
- C-class labels have lower value and can be managed with less scrutiny.
Inventory Management for Industrial Labels
When inventories are managed efficiently, a manufacturer can slash the TCO of their durable industrial labels and grow the bottom line. An effective label inventory management program involves a combination of proactive strategies to reduce TCO including:
- Avoiding line stoppages
- Reducing obsolescence
- Accurately forecasting demand
- Minimizing rush orders
- Implementing VMI
- Embracing digital production
- Standardizing label SKUs
- Classifying labels through an ABC analysis
Label TCO Blog Series Concludes
The seventh and final blog in this series will be devoted to ongoing process improvement. Join us in a few weeks on the Taylor.com blog as we conclude our exploration of the factors influencing TCO for durable industrial labels.
Taylor: Inventory Management Excellence
Taylor possesses world-class logistical capabilities for label programs of all types. For example, we offer mobile-ready vendor managed inventory services that allow you to meet spikes in demand as they occur while keeping TCO to an absolute minimum.
To learn more about Taylor’s expertise with durable labeling solutions – including inventory management services – please contact one of our labeling experts.