This is the second installment of our five-part series called Labels 101: Five Key Elements of Effective Labels.
How to avoid getting stuck with the wrong adhesive
When a label does not stick under expected conditions, the consequences can range from a branding blunder to the risk of physical injury. Yet, the choice of adhesive is not as simple as finding the strongest one available — an adhesive that sticks to a glass test tube may not stick to a plastic one. That’s why it’s vital to understand adhesives. Let’s begin by examining the basic types.
Types of Adhesives
Label adhesives are divided into four types:
- Permanent adhesives cannot be removed without distorting or destroying the label or the surface to which it is applied. The right choice of permanent adhesive will depend on the substrate and surface material, whether the surface is curved or flat, as well as environmental conditions including UV exposure, moisture, temperature range, and contact with chemicals.
- Removable adhesives are sometimes used on retail goods. Adhesives used on clothing tags, for example, are designed to be removed without leaving a residue. Other adhesives can be removed with soap and water, such as the stickers for glassware.
- Repositionable adhesives allow labels to be removed and reapplied many times over a long time span, usually on flat surfaces, making them ideal for large applications that require careful placement. Temporary sticky notes are another common repositionable adhesive.
- Cold temp adhesives are used for labels designed to be applied to cold surfaces, typically below 25°F.
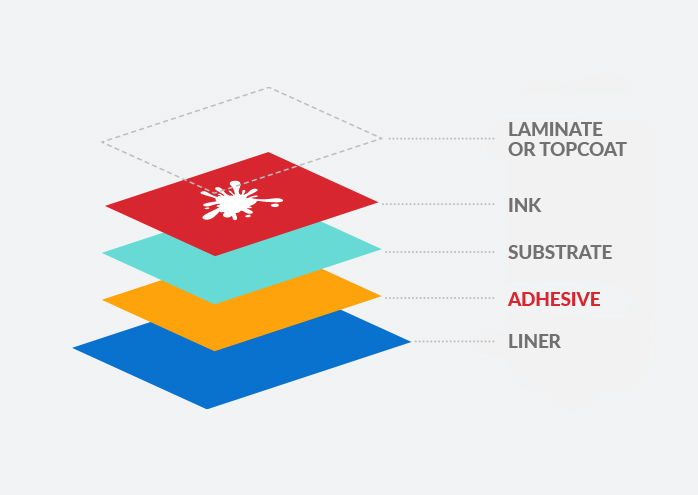
Adhesive performance factors
Regardless of type, all adhesives have three distinct performance factors:
- Tack is the initial attraction of an adhesive to a surface with minimal external pressure.
- Adhesion is the bond strength between the adhesive and the surface after pressure has been applied to affix the label.
- Shear is the amount of time required, under specified test conditions, to slide a standard area of pressure-sensitive label from a standard flat surface in a direction parallel to the surface.
With all the factors above, knowing what kind of surface the label is to be affixed to is critical. An adhesive will hold or release differently on a smooth surface like glass than on a suede fabric material.
Acrylic vs. rubber-based adhesives
Another important distinction among adhesives is choosing between acrylic and rubber-based chemistry.
- Acrylic adhesives are noted for long-term bonding and UV resistance in outdoor applications. They also offer excellent resistance to most common chemical solvents. Acrylic adhesives may have higher initial costs but offer superior durability.
- Rubber-based adhesives are widely used for short-term general purpose indoor applications because of their instant bonding and low costs. However, they are susceptible to common chemicals and UV exposure.
Tamper-evident adhesives
When used with the right substrate, a tamper-evident adhesive reveals attempts to remove the label by shredding or revealing a hidden security message such as “void” in the adhesive. Tamper-evident labels are often used for retail pricing, pharmaceuticals, warranties and other applications where it’s crucial to deter the removal of the label.
Shipping and storage of adhesives
Shipment and storage are also critical components of label performance. To avoid oozing, labels with thick adhesives should not be stacked high enough to create excessive pressure during shipping and storage. Because of their short shelf life, it’s best to keep a low inventory of labels with a thick adhesive. High heat can also adversely affect adhesive. It can soften adhesive and create oozing and often requires special handling in hot climates or during the summer months.
Making the right choice
The right choice of adhesive can be the difference between a label that sticks for its intended lifetime—at the lowest possible costs—and one that fails to adhere. Yet, your choice of adhesive is just one part of the formula for creating the right label.
Selecting the right adhesive, and other label components, is a complex process. Partner with a knowledgeable label supplier to make the right choices for your specific needs. Your label partner can also review your current labels to ensure the right balance between performance and cost.
To learn more about the other key components of an effective label, read these posts in our “Labels 101” series:
- Choosing the Right Substrate
- Choosing the Right Liner
- Choosing the Right Ink
- Choosing the Right Laminate
For more information on how to manage your print effectively, including labels, read about PrintStack, the Operating Model for Print.