Understanding labels is vital knowledge. A label is more than an effective brand ambassador. When used for critical information, a label’s failure in legibility, colorfastness or adhesion can create significant financial loss and even the risk of injury. It is important to know the proper components to choose for your label’s particular usage.
We kick off our five-part series called Labels 101: Five Key Elements for Effective Labels with a disccussion of the first element: substrates.
What is a substrate and why is it important?
Put most simply, the substrate is the base material on which the label is printed. Of the five elements this blog series will examine, the choice of substrate can potentially have the greatest impact on cost, adhesion and legibility. The first decision when it comes to substrate is the choice between paper and synthetic.
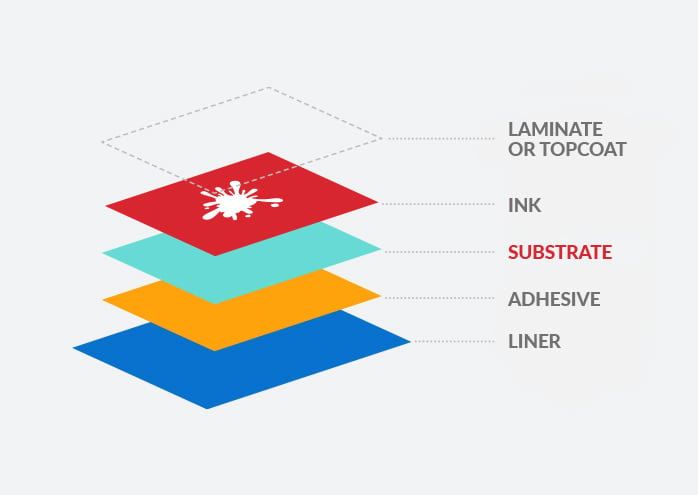
Paper or synthetic—what’s the right choice?
While paper and synthetic are the two basic choices, options for both abound. One common element between paper and synthetic substrates is a wide array of thicknesses, making the label flexible enough to mount on a curved surface or rigid enough to lay flat. Let’s examine the differences between paper and synthetic in more detail.
Paper substrates
Paper substrates are typically used for indoor labels with a relatively short lifespan and limited exposure to moisture, chemicals, temperature extremes and abrasion. However, paper substrates can be combined with a synthetic laminate for additional permanence. Topcoats such as varnish or aqueous coatings can also be used to make paper more durable. If your label requires customization from a secondary printer, paper is often the best choice—although secondary customization is also possible with synthetics. Paper comes in coated and uncoated finishes and is available in a wider range of colors than synthetic substrates. In general, paper substrates cost less than synthetic ones, often making paper the best value for less demanding applications. Many paper substrates can use recyclable material, making them more eco-friendly. However, the substrate will not usually be biodegradable once an adhesive has been added.
Synthetic substrates
Synthetic substrates are typically used for most outdoor applications or indoor applications with exposure to a variety of harsh conditions. Most synthetic substrates are clear, metallic or white.
- Polycarbonate is considered the top of the line synthetic substrate and can last for years without fading under extended exposure to UV light while providing resistance to moisture, many chemicals and abrasion. Available in matte, gloss and satin, polycarbonate can even be embossed to create buttons. Polycarbonate films are frequently used for control panels and displays due to their durability and appearance. Typically the polycarbonate films used are in the range of 5-10 mils thick.
- Polyester is durable but rigid and can typically provide two to five years of outdoor service. Polyester films are available in a wide range of thicknesses starting at 1 mil.
- Vinyl substrates conform well to curves and provide an outdoor service life of seven-plus years. A 4-mil vinyl is the most commonly used thickness.
- Polypropylene is moisture resistant and temperature variable, making it popular for consumer goods like plastic soft drink containers. With a useful lifespan of approximately six months to two years, polypropylene is used for a number of indoor or short-term outdoor applications. Polypropylene films are typically less costly on a unit area basis than other films.
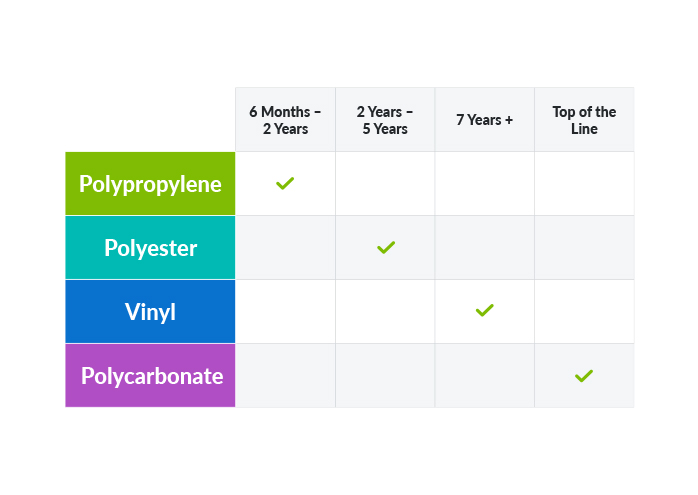
Subsurface printing
With subsurface printing, the imaging takes place on the back side of a clear synthetic substrate. Typically there is a white or colored ink printed to provide a background color. The need to subsurface print sometimes determines the type of material used. The advantage of subsurface printing is that the substrate acts as a protective layer, making it more cost-effective than using a laminate in many cases.
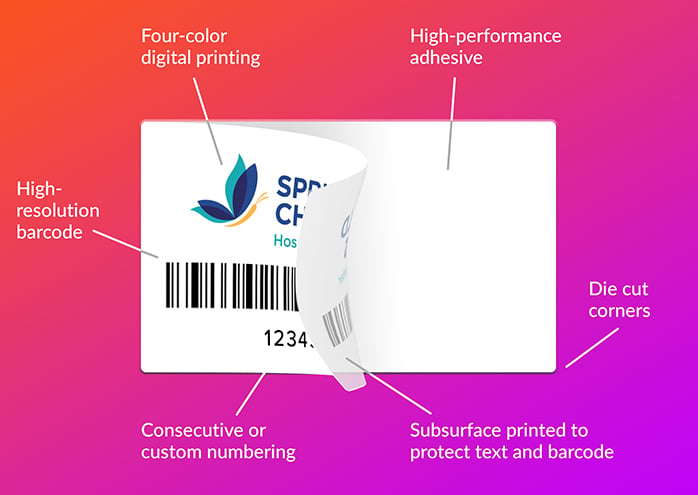
Making the right choice
Choosing the right substrate will ensure your brand and safety messaging lasts for the life of the product. However, the wrong choice can lead to loss of legibility and adhesion, creating failures that can be potentially catastrophic. Your choice of substrate is a key part of the formula for creating the right label.
To learn more about the other key components of an effective label, read these posts in our “Labels 101” series:
- Choosing the Right Adhesive
- Choosing the Right Liner
- Choosing the Right Ink
- Choosing the Right Laminate
For more information on how to manage your print effectively, including labels, read about PrintStack, the Operating Model for Print.